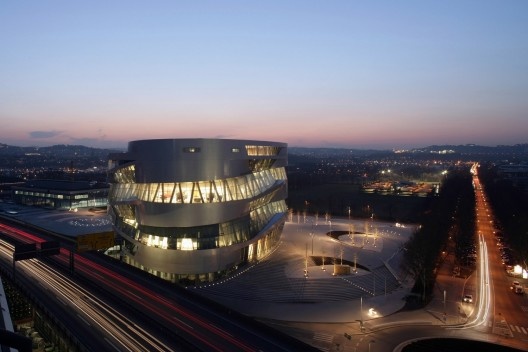
Mercedes Benz Museum
Foto divulgação [UNStudio]
GC: Can you tell me about your teaching activity at the Academy of Fine Arts in Stuttgart? What are you teaching there?
TW: The Academy of Fine Arts is a very special place. Usually in Germany you have the big technical universities and then you have the universities of technology, which formerly were even more technical, but there are only two academies in Germany where you can study architecture as a Bachelor and Master program, and this is a very artistic way of looking at it. What we try is to allow people to find their own approach to architecture. So we are not just teaching students how to do something; we want to make students interested, and then they will become motivated in learning how to do it. I teach in the Master program. It's a studio about different types of spaces very much related to the use of diagrams, trying to abstract or to visualize the underlying relationships and connections in a design and to create something that you wouldn't create based on your cultural background or your experience. To allow people to develop something without knowing exactly what they want to do. I also teach a course on digital design. The idea is to show people the full loop, how to design a complex geometry, how to build prototypes using CNC machines, learning what works well and what doesn't, and the limitations of the CNC machine, and then adapting your digital model again, and then develop a final project. So what we are trying to do is showing students that there are interesting elements in every part of the process, as long as you work in a loop. The process is not linear; it is a recursive process. It does not matter anymore if you start top down or bottom up. When you move through the whole cycle you have to combine both approaches. You need to have an idea, but then the idea needs to materialized in details and every detail needs to be manufactured. Then, from the manufacturing, you have some ideas about the concept, if that was the right concept or if you have to adapt the geometry or even the concept. So it's very much teaching a method. How to work rather than what to do.
GC: Do you bring a lot of input from your office in Berlin to the studios that you teach in Stuttgart?
TW: As a practicing architect you can apply the knowledge that you develop in the office and this work between analysis and synthesis you can really apply in the courses and our practice also benefits from this more theoretical approach that can be done in the studio. For instance, we always look at the manufacturing possibilities in the use of certain machines. For instance it's quite amazing how when using 3D printers people think that you don't have to care about the geometry, you just push a button and you can build any 3D geometry. But this is partially true. There are also limitations in the fabrication of 3D-printed models. What I think would be even more interesting to say this model is going to be built in layers, so how can we use the layering as something which becomes like your fingerprint. The manufacturing process is visible in the final product, as a feature or as a quality of the final product, rather than trying to print something that looks totally flat as a surface. We are looking at the capacity of the 3D-printer to be used also as an aesthetic asset. We named it 3D fingerprints. You can manufacture the same geometry, but if you print it at a different angle things may look slightly different, and rather than that being simply something that happened you should design it. It's a decision that you make. You should be aware of it and should be able to take into account when you design the object. If you need to split up an object into smaller parts you have to think about the seams and turn them into a feature rather than into a necessity.
GC: What is your opinion about the education of architects in Germany? Which new technologies are effectively being incorporated in the professional training?
TW: Of course it's important that you learn to use a variety of tools. How to put information into the computer and how to get information out of it. But people end up learning that somehow. In my point of view what is more problematic in education is that we are still educating people in the 19th century view of the creative architect. The guy that has some idea, and creation is something personal, you do the design and you have other people who help you to execute it. This is a very old-fashioned idea of the architect's work. It's much more about the collaborative process, where everyone contributes different skills and knowledge. In the practice it's much more about the collaboration between architects and engineers. You need to learn a language to communicate with an engineer. This language is programming, then this is fantastic, but it does not work for everybody. But usually one person knows programming and another person knows about something else and they need to communicate about the project. So I think the most important is to teach a way of communicating within a team of architects or of architects and engineers. Communication is the most valuable part and that is something we are not giving enough [attention]. We teach skills and crafts but we also need to teach how to make decisions. We should also teach culture, architectural culture. Not only the history of architecture, but the history of manufacturing, the history of designing, understanding that technology is important, it makes it possible to do things differently. But I'd like to cite Cedric Price: "if technology is the answer, then what is the question?" So in the end we always have to ask ourselves why are we doing this, because it is something for people. We should not design a building because we can push a button in this fantastic new tool which allows you to design a building that looks like this or that. This is fine for the academic environment, it's a starting point, but it should not be your goal in life to build this double twisted crazy thing. To leave a trace as the guy who did the most trendy shape. But how can we assemble all these skills to make something that makes sense? And that is something that I often think we don't have enough time to come to this point. We are so busy trying to teach the basics that we never talk about what do you do once you acquire the basics.
GC: Are you doing research at the School of Fine Arts?
TW: We are a small school with limited budget, so we cannot set up a very large fabrication facility. We have small machines and we do research on the basics. One example is [what I described before about the 3D-printer]. Another thing we did with a very simple 3-axis CNC mill, is to hack the code of the milling path so that you don't need to design a lot of polygons to have a very complex surface. We design a simple surface and then we hack the code to instead of having the machine milling it smoothly, we program the sequence in which it attacks the material, and the result is based purely in the [fabrication] process and not in the geometry. What we design is actually the movement of the mill and its traces become materialized in the object. So we are looking at, as an architect, where can you interfere in the process of manufacturing. It's the opposite of saying that firstly we produce some complex geometry and then we find a better machine to produce that complexity. It's more about using a simple machine but increasing the complexity of the result by making it in a different way. It's like hacking. When I worked in my Commodore 64 the computing power was so little that I constantly had to be creative about the way of using the storage. We were very much looking into the process and how to reuse things and how to minimize capacities. I believe this is suitable for an academy where we don't have the funds to buy the latest equipment. But we also collaborate with other people. We had a robotic workshop with TU Graz, in which we did styrofoam cutting, looking at how we could use the robot to minimize the waste.