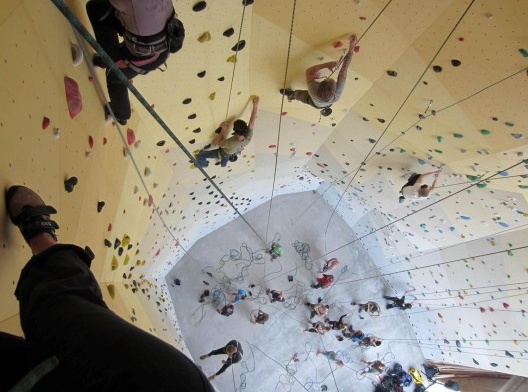
Parede de escalada ONL [ONL]
MS: Have you used 3D printing technology for a building?
PS: No. It’s difficult. There is a big jump from the current state of printing and additive manufacturing to having production level high-quality elements. I think that is, actually, one of the main issues with the maker revolution. You can have a 3D printer, you can have it at your house, but the question is: what kind of product you can make with that? It is very limited at the moment, because the technology is not that far advanced to make high end product with it. That is one of the main issues also to transfer that to the building process and to actual build structures; because it is really difficult to get enough strength and to get a good enough finish basically. We are experimenting on different levels with that, but it is really hard to get to a level that is feasible. Also, if you compare the production time that it takes to do that is expressive. My colleague Gijs Joosen did a lecture while ago; he did a comparison what it would take to make the A2 cockpit building, to make the complex geometry of the nodes. It would take 9375 days, instead of 13 and cost 40.500.000€ instead of 135.000€ if they would be made in 3D printed steel instead of construction steel with file-to-factory production.
It is interesting also looking at 3D printing you can make your custom node, and make it really ornamental. This can take the idea that the detail becomes the architectural ornament to the next level. It can become completely purposefully designed, there is only material where it is needed to guide the forces and connect the different elements.
There is a really big gap to bridge from using construction methods that already exist and you adapt them by starting to control them digitally. Having actual production level methods or using this additive manufacturing elements and adapting them in such way. It requires a different way of thinking. There is a huge potential in existing methods as soon as you start to rethink them. It is not so much about reinventing the wheel. The actual production method is much more about reinventing the process.
MS: That is a very good answer. I also think we have a long way before the 3D print technology become cheaper and available for construction.
PS: Even then, it is questionable if it would be possible to shorten production time. To make sure that you can have the ease and the equipment of production that you have in other digitized production methods. Also in this comparison, this nodes and the structure was made in 30 days and if you print in steel that it would be almost 10.000 days. That kind of time difference is a gap that is hardly bridgeable. It is far more interesting to create a way of opening up the industrial production process and make that accessible digitally, and controllable digitally. So you can actually start doing your free form design, your different types of design, and you even allow the end user to design with that high level industrial production methods. Rather than giving everybody a 3D printer and allow them to design plastic things. So that is also what we are developing now, more a sort of product. We have a lot of projects at the moment, but we do more products like design. We have done a system for climbing walls for example, which I am very much involved.
Basically, we made an application in which you can design your own climbing wall and that is connected to a whole processing pipeline in Grasshopper with which we create all the production geometry. So we can actually sit with the person who wants to have a climbing wall, having a script running and we have a design environment that direct feedback the angles and the shapes of the surfaces. You have a full 3D view of what you actually doing and also give you direct feedback on the elements, if they are correct and if they have the right angle and if they fit within the complete bandwidth of the system all the way up to the production, so all the parameters are incorporated into that. You can start shaping the complete wall and even with that application somebody could do that at home or on an iPad, and then send it to us and we start working and directly make a producible design. It is a completely freestanding 3D shell that you create; it is completely digitally manufactured and delivered on site. The only thing that you have to do is pull it together and you get a 3D shape.
MS: You talked a little about ornament. Do you think that new technologies could bring a new type of ornament or aesthetics?
PS: It does. As I would see it, it shouldn’t become additive. When it becomes an integrated strategy then actually I think it becomes really aesthetically pleasing, the detail becomes the ornament. For instance, in the A2 cockpit or maybe in the climbing wall the fully integrated structure becomes an aesthetic, becomes the ornament. The detail or the design becomes the ornament. This is the backside of the climbing wall but has some interesting aesthetic. That also is very different in the way we approach to other offices do, then the ornament often becomes an overlay or addition. Of course, digital techniques always allow you to do that, but then it is merely functional as a façade layer or a dress. The full integration of that, the actual detail becomes the ornament itself and you get a full integrated aesthetics as well in terms of structure skin. The whole building starts to become one fluid integrated design.
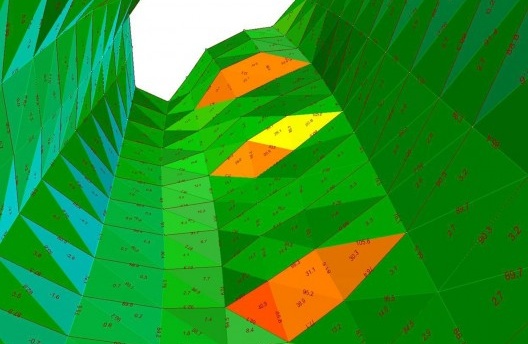
Projeto da parede de escalada [ONL]
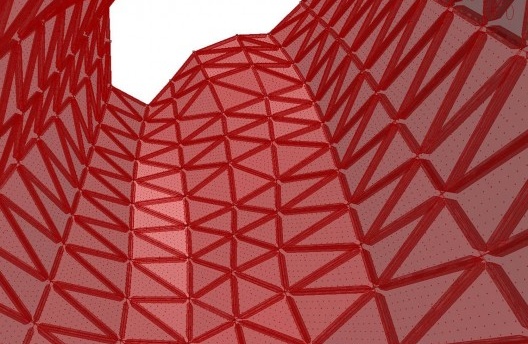
Modelagem da parede de escalada com detalhamento estrutural [ONL]
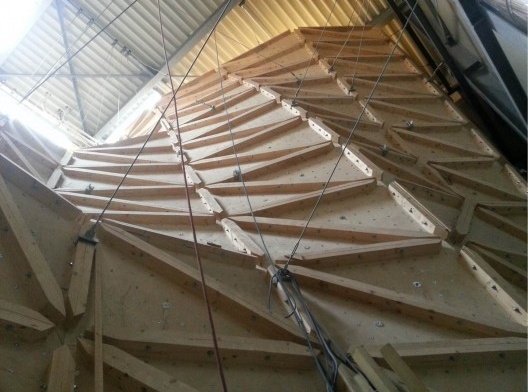
Fabricação da parede de escalada [ONL]