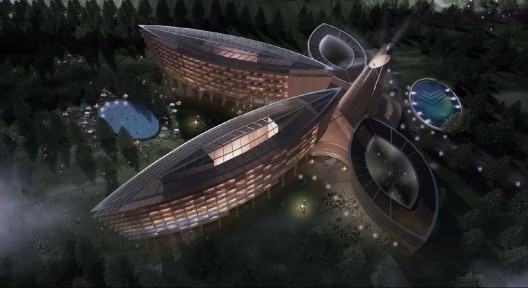
Mriya Sanatorium, Criméia. Tabanlıoğlu Architects / Foster and Partners
Imagem divulgação [Website Metta]
Wilson Barbosa Neto: In the roofs you showed us, what other digital fabrication processes were used in regards to the steel structure?
Peter Mehrtens: When multiple trades [in the same building] use a digital approach it will usually ensure that all parts are fabricated precisely, but that doesn’t always assure assembly on site with the same quality. In a train station in Austria [for example] the steel structure was plasma-cut. In the project in Taiwan the steel structure is being done with substantial labor; especially in the sub-structure there is not so much digital fabrication happening as it could be. I think that is where the future is going, but it usually depends on where it is being produced.
WBN: Do you use digital fabrication techniques also to create scale models during the development of the designs?
PM: To clarify detailing we sometimes create mockups. These are usually in scale one to one. If it is a sub-structure this is usually hand made. So, that would be a no. If we create panels for a mockup they are digitally produced, so in that case yes. However, if we are talking about the design stage issues, what I have looked into is 3D-printing at the design stage in small scale, but that is only for layouts. Recently we have actually used 3D-printing to investigate when developing new parts and components, system components for sub-structure parts, before milling them in aluminum and then, when we have them finalized, having them produced with a customized tool, in terms of metal tooling. So we use digital prototyping technologies for in-house product development research.
Gabriela Celani: Can you please describe the work that you and your wife do at DesignToFabrication?
PM: DesignToFabrication creates customized cad plugins for fabricating industries, architecture, engineering and construction firms and industrial designers. The challenge is to create tailor made solutions that focus on specific fabrication processes and therefore are usually not placed in the public domain. Majority of work is on scripting custom components that extend Grasshopper / Rhino and to create scripted models of building envelopes.
GC: Who are your typical clients, why and how do they look for you?
PM:Contact to most clients came along via teaching. The majority of outsourced design related tasks in industrial design or automotive industries are conducted under NDA (non-disclosure-agreement), so we usually have to work under cover. We have no website, which grants us their trust, that we treat clients data strictly confidential.