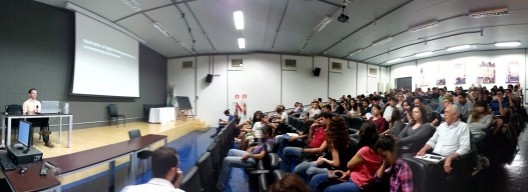
A palestra de Peter Mehrtens na Unicamp sobre Application of Digital forming Processes in Contemporary Architecture reuniu uma centena de expectadores
Foto/Photo Gabriela Celani
Wilson Barbosa Neto: Why did Bemo hire you?
Peter Mehrtens: The hiring came via teaching. I was teaching parametric CAD, Grasshopper, direct modeling with Rhino and scripting in part time. Some of the people in my class were technicians and architects who were working for Bemo, and they recommended me and Bemo got in touch with me. I was impressed by the drive for new technologies at Bemo. They had developed together with the machine fabricator this new machine, however there was no algorithm to create the data that drives it and no experience of how to create the building envelope for free-form buildings. So that was a coincidence that I had something to bring in and they had some interesting challenges.
WBN: Why does Bemo have a design team? What is the importance of having an architect inside a factory?
PM: The main reason is that the complexity of free-form building envelopes requires some knowledge of generative design, but also constructive detailing, and sometimes the design architects who create the conceptual design don’t have the resources in their offices to bring along this specialist design topics. Bemo already had a technical design team, which supported detailing and structural issues etc., and this is being expanded now to office support for free-form buildings and generative design.
WBN: So it’s like bridging the gap between fabrication and architects?
PM: It’s exactly that! There was a gap of knowledge to bridge the fabricator and the design office. And of course there are different ways of going about it: you can outsource it or you can have it in house. It is related not only to [the economic] sustainability of employees, but also to having a team that feels like they belong there. This is why their approach is not to outsource.
WBN: Can you describe how many people work in your design team? Are they architects or what is their background? Are there any students working as interns?
PM: There is a mix of professions in the design team. We have architects, civil engineers, drafters and state approved technicians (a draftsman that has supplementary education, with very intensive detailing background). We also have some students who are studying façade technology at a nearby University of Applied Sciences. They work and study; they stay at the office for three months then they are at school for three months. It’s a technical program.
WBN: In what stage do you usually jump in during the design process?
PM: Thanks to the modularity of the [Bemo] components I’m able to help in the conceptual design, helping in the modeling for the execution since an early stage. However, not all projects are brought to my design team in the same stage. It’s very different from project to project. It sometimes happens that it is as late as it has already been tendered , then it’s really difficult to roll back and to modify things. And sometimes it’s in a pre-tender stage. And we had some projects in which I thought it was most fruitful and the collaboration was best when we worked together as early as possible. For example, we’ve been doing that for Foster and Partners. We’ve also been working with Mecanoo for a number of years now, in the Taiwan project, a railway station. The earlier, the easier it is to express and explain all the dependencies. Sometimes it ends up offspringing parametric design to architectural design offices, which up until then had been drawing conventionally.